From affected person information to an end-use prosthetic system at Quorum Prosthetics
At 12, Joe Johnson misplaced his leg in a motorbike accident. He confronted preliminary challenges with a fundamental prosthetic till he found how AM might assist produce a tailored and extra snug 3D-printed prosthetic. Johnson’s story might have ended after he received his first prosthetic, however he didn’t see anybody prepared to take the dangers to assist amputees. His journey subsequently led him to discovered Quorum Prosthetics, a prosthetics firm that makes prosthetic legs and arms, {custom} bracing, and the Quatro adjustable 3D printed sockets. Over time, the corporate has been constantly exploring the usage of digital manufacturing applied sciences to offer amputees the proper match. If we’re speaking about it as we speak, that’s as a result of Johnson’s expertise allowed us to know the digital manufacturing levels of 3D-printed patient-specific gadgets.
Quorum Prosthetics itself is a journey of resilience. We share its story as we speak as a result of “Additive Manufacturing is a car to [its] concepts” – within the phrases of Johnson. Nonetheless, in 1998, when the corporate was based, it wasn’t. It took Johnson a number of funding, vitality and belief in engineering experience to convey his firm to the place it’s as we speak – sure, as a result of Johnson just isn’t an engineer by coaching.
“I had this recipe 8 years in the past of what I needed Quorum to realize. We needed to standardize design for prosthetics because it was tough to fastidiously replicate present ones. [From conventional manufacturing techniques such as lamination resin and plaster, we took the leap to AM in 2019. Today, with a distributed manufacturing model, we can help amputees beyond our frontiers]”, the founder provides.
On a extra sensible be aware, it’s necessary to know that regaining mobility hinges on having a prosthetic system that’s each purposeful and correctly fitted. A traditional manufacturing course of would require the usage of a plaster forged personalized for the affected person and lamination utilizing carbon and resin. “The issue is, despite the fact that the ultimate socket is snug, the manufacturing course of is inaccurate for replication”, Johnson informed 3D ADEPT Media. To not point out that the form and quantity might change over time, inflicting a type of stress or discomfort on the wearer.
The Quatro socket from Quorum Prosthetics is predicated on a patented design that permits wearers to adapt the amount and compression utilizing adjustable reels and interchangeable consolation cells. The reality is the method to get there calls for a meticulous and complete digital workflow. Commenting on the event of such patient-specific gadgets within the realm of prosthetics and orthotics, Johnson explains that every step of the digital workflow is “crucial to make sure the creation of prosthetic sockets, such because the Quatro socket, that seamlessly combine with the affected person’s anatomy, optimize consolation, and improve performance.”
What are these steps?
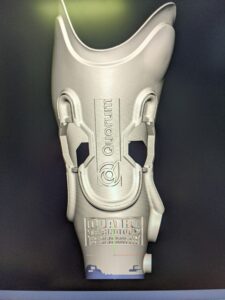
On a really technical degree, the digital manufacturing levels could be gathered in 3 major steps:
- 3D scanning & digital mannequin creation
- Print & course of
- Affected person becoming
At Quorum Prosthetics, the complete manufacturing course of from affected person evaluation to final result analysis takes 10 steps. These steps embody:
- Affected person evaluation: Any healthcare supplier would agree with the truth that this step is apparent because it provides a greater understanding of the affected person’s particular wants and necessities, and helps to collect related medical information akin to residual limb measurements, pores and skin situation, and purposeful capabilities.
- 3D scanning: With this the first step can seize the form and contours of the residual limb precisely. Normally, Computerized Tomography (CT) scans, Magnetic Resonance Imaging (MRI) scans, X-rays, and handheld 3D scanners could be utilized to seize the small print of the affected person’s anatomy. This digital illustration turns into the inspiration for the next steps within the AM course of.
Quorum makes use of an Artec 3D scanner to carry out this process.
- Digital mannequin creation: Thereafter, the designer makes use of a particular software program resolution to transform the 3D scan information right into a digital mannequin. Sure changes based mostly on the affected person’s anatomy may also be made at this stage.
-
Legend: Changes could be made with pinpoint accuracy. Credit score: Quorum Prosthetics . Socket design: The extent of sophistication within the design software program is essential right here, because it dictates whether or not the method stays a guide craft or progresses towards partial or full automation. This digital modeling section permits unparalleled precision, guaranteeing that the eventual prosthetic seamlessly conforms to the person anatomy and necessities of the affected person.
With the assistance of Geomagic Freeform, they’ll design the socket and combine options akin to pressure-relief areas, suspension mechanisms, and reinforcement. Johnson defined that they held a patent for the Quatro socket, which had exact design necessities, and Freeform was a super resolution for assembly these necessities. Primarily, Freeform allows them to create custom-fitted sockets for particular person sufferers, leading to distinctive shapes for every. Nonetheless, the standardized format of adjustment traces and the complete Quatro system in Freeform streamline the design course of, making it environment friendly and easy. Most significantly, via typical strategies, creating a socket design of this nature might require as a lot as 12 hours. But, the Quorum crew can finalize a design in a fraction of the time, sometimes inside 4 to 6 hours.
- Manufacturing preparation requires as an illustration to substantiate that every one digital fashions are inside the boundaries of the print mattress.
- Fabrication: Quorum depends on HP Multi-Jet Fusion to fabricate its sockets. Another AM course of may very well be assessed to make sure that the tip half is biocompatible and that it delivers the perfect power and weight. That being stated, there are necessary variations on the geometry degree when one compares a socket that’s historically made and one that’s fabricated with MJF. Different variations embody connection factors and thickness (Carbon fiber to have 6mm uniform thickness leveraging 4 layers of fiber weave and a couple of bases of resin.)
-
Legend: The Quatro is strength-tested utilizing ADAC’s metrology lab, making certain a protected socket expertise every time. Credit score: Quorum Prosthetics High quality management: Past assembly high quality requirements and specs, it’s about making certain accuracy and luxury for the consumer. It ought to be famous that no official testing protocol exists to check socket efficiency. That’s why healthcare suppliers typically depend on numerous testing methodologies. ISO 10328:2016 as an illustration specifies procedures for static and cyclic power checks on decrease limb prostheses which usually produce compound loadings by the appliance of a single take a look at power. The compound masses within the take a look at pattern relate to the peak values of the parts of loading which usually happen at totally different instants in the course of the stance section of strolling.
- Meeting & customization: Aesthetics and purposeful necessities ought to be met at this degree.
- Becoming and adjustment: After becoming the socket onto the affected person’s residual limb, a few changes can nonetheless be made. When required, Quorum as an illustration provides consolation cells into the perforations of the versatile interior socket to offer the affected person with extra cushion.
- Final result analysis: all through this course of, the Quorum crew follows up with the affected person to evaluate the efficiency of the system in real-world eventualities.
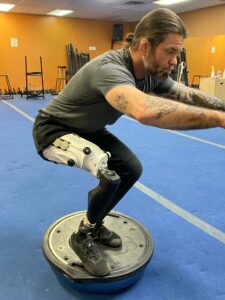
Concluding ideas?
Whereas healthcare suppliers would possibly face labor shortages and measurement capability when counting on AM, the benefits of utilizing the expertise for 3D printed prosthetics are these you would possibly already be aware of, if you realize the expertise: customization, improved consolation, lowered manufacturing time and cost-efficiency.
As a matter of reality, as regards the price issue, Quorum’s adjustable sockets can now be coated by insurance coverage corporations underneath prosthetic quantity adjustment.
As AM continues to evolve, it can proceed to reshape the prosthetics panorama, providing newfound accessibility and enhancing the general welfare of people in want. With greater than 57.7 million folks residing with limb amputation resulting from traumatic causes worldwide, I hope to see extra “Quorum Prosthetics” emerge the world over.